VulcanoClean
LCM vulcanisation lines using the VulcanoClean® process
Salt bath technology is recognised worldwide as the best process for the continuous vulcanisation of elastomer profiles, not only for its heat transfer capacity, temperature homogeneity and ease of use, but also for the quality of the resulting surface appearance and mechanical properties, and for its ability to vulcanise all polymer blends
Since MDC Engineering S.a.r.l. in France, in cooperation with Durferrit® GmbH in Germany, revolutionised salt bath lines at the end of the 1990s, making them extremely modern, efficient and safe, many new applications have emerged. What’s more, thanks to new peroxide mixes that can generally only be vulcanised in a salt bath, productivity levels unimaginable 20 years ago are now being achieved
Thanks to the VulcanoClean® process, the environmental and energy aspects which, twenty years ago, were a weak point in comparison with the competing technologies of the time, such as hot air + microwaves or hot air shock systems, are no longer so. By eliminating pollutant emissions and using submerged heat exchangers for combined electric/gas heating, this process offers the best energy efficiency and the best environmental technology
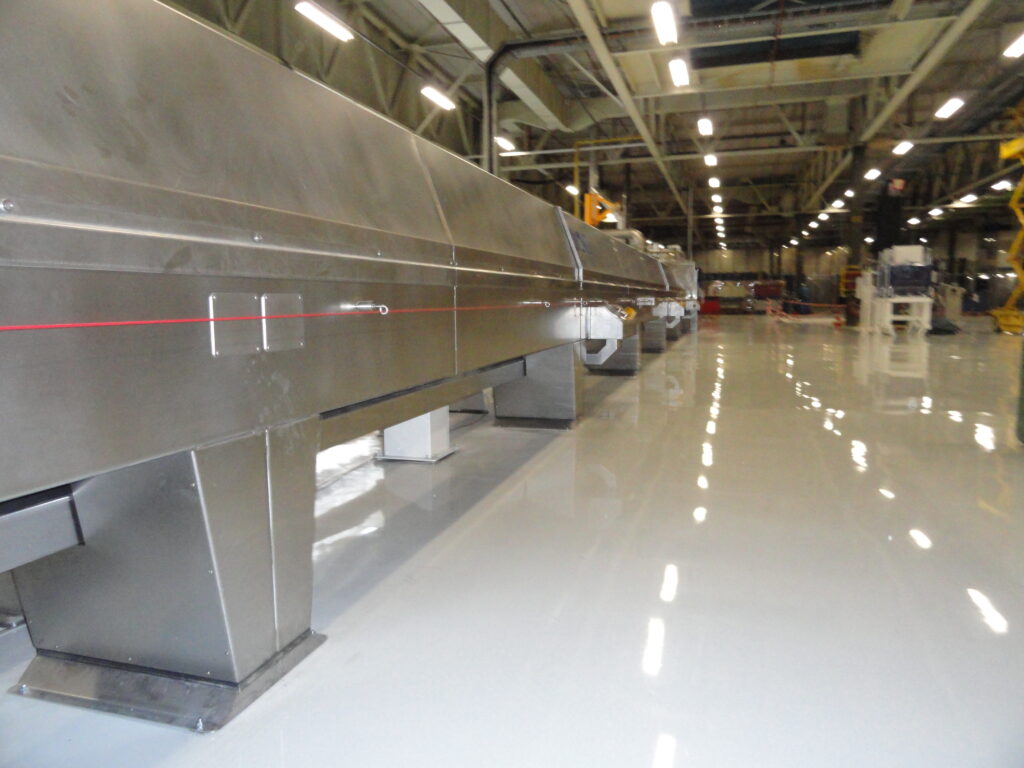
Main functions
The installation consists of a long salt bath, known as the “vulcanisation tunnel” (Part 1), combined with a highly efficient washing and cooling system, known as “Ecoclean” (Part 2), with the aim of guaranteeing rigorous washing and recovering 100% of the entrained salt.
This “Ecoclean” is combined with a gas-heated (or alternatively electrically heated) evaporator oven, known as the “SWV oven” (Part 3), with 3 main functions:
- Achieve continuous circulation and filtration by eliminating carbonates.
- Heat the salt from the entire line in working conditions.
- Treat the salt in a closed circuit using a highly sophisticated double-chamber system and be able to depollute the concentrated washing water by evaporation.
The salt is continuously circulated between the “SWV oven” and the “vulcanization tunnel” by means of immersed tubes. The tunnel temperature is thus maintained by gas heating, making the VulcanoClean® system even more economical. Salt contaminated by floating particles and organic impurities in suspension is returned to the SWV oven, where it is filtered and treated before being recycled into the line.
On leaving the vulcanisation tunnel, the profile passes through a patented washing and cooling machine called Ecoclean, which cleans and captures 100% of the entrained salt for purification and recycling. Thanks to the VulcanoClean® process, new salt is added in proportion to the volume of solid sludge eliminated by the system.
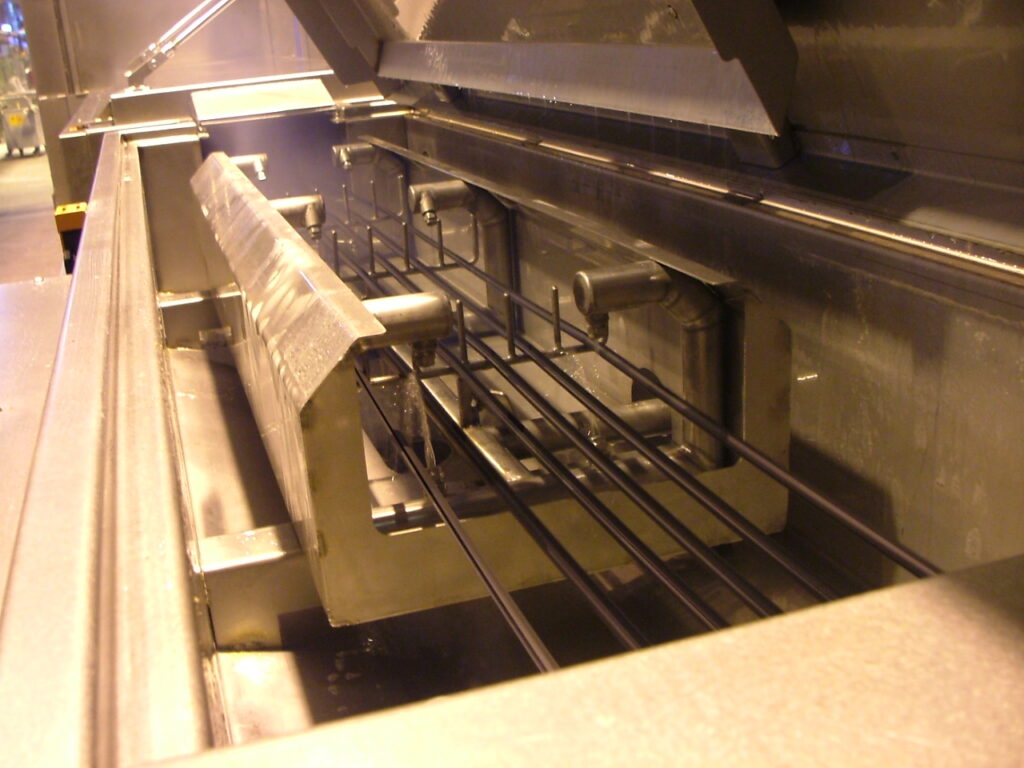
The VulcanoClean® process offers the following advantages:
Work at a constant salt level.
Better heat exchange and greater temperature uniformity.
Continuously collect any impurities that form.
Significantly reduce the risk of clogging liquid salt spray systems.
Rigorously wash, cool and dry all profiles.
Significantly reduce salt consumption (in relation to the volume of sludge).
Significantly reduce water consumption (between 20 and 40 times less).
Optimise and reduce energy consumption as much as possible.
Automate production as far as possible, while minimising start-up and maintenance operations.
Eliminate the risk of fire.
Treat atmospheric emissions.
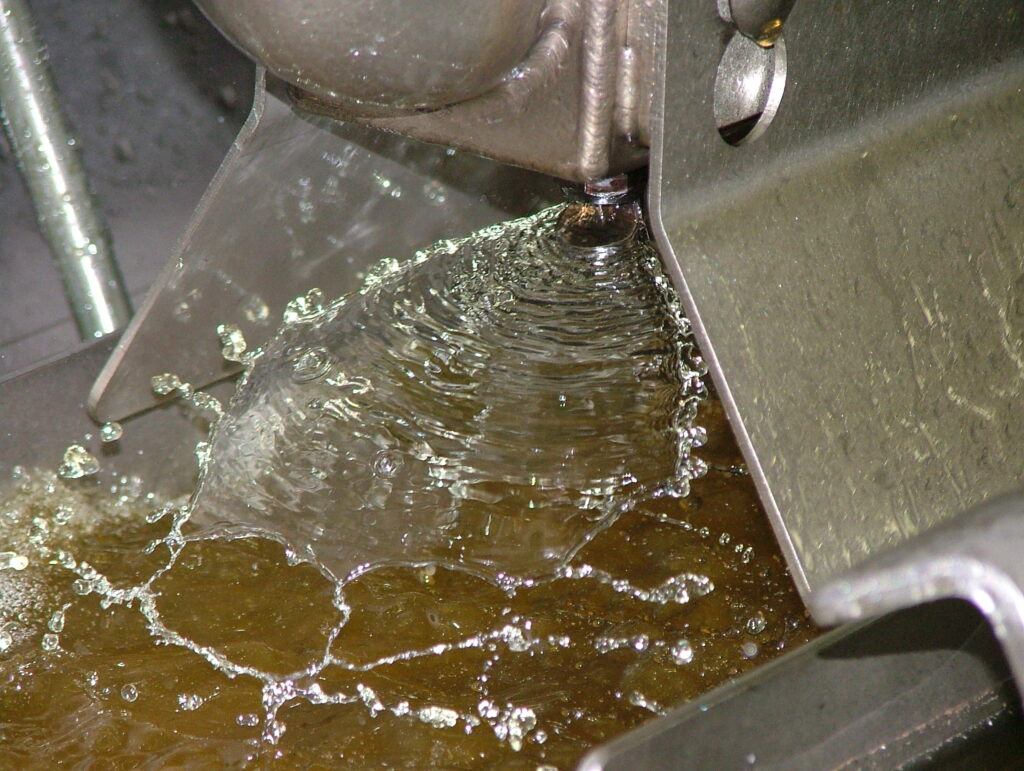
High-tech and economy versions
With the ambition to catering for all budgets, MDC Engineering offers its VulcanoClean® process in a standard “high-tech” version and a more economical version called EVSB.
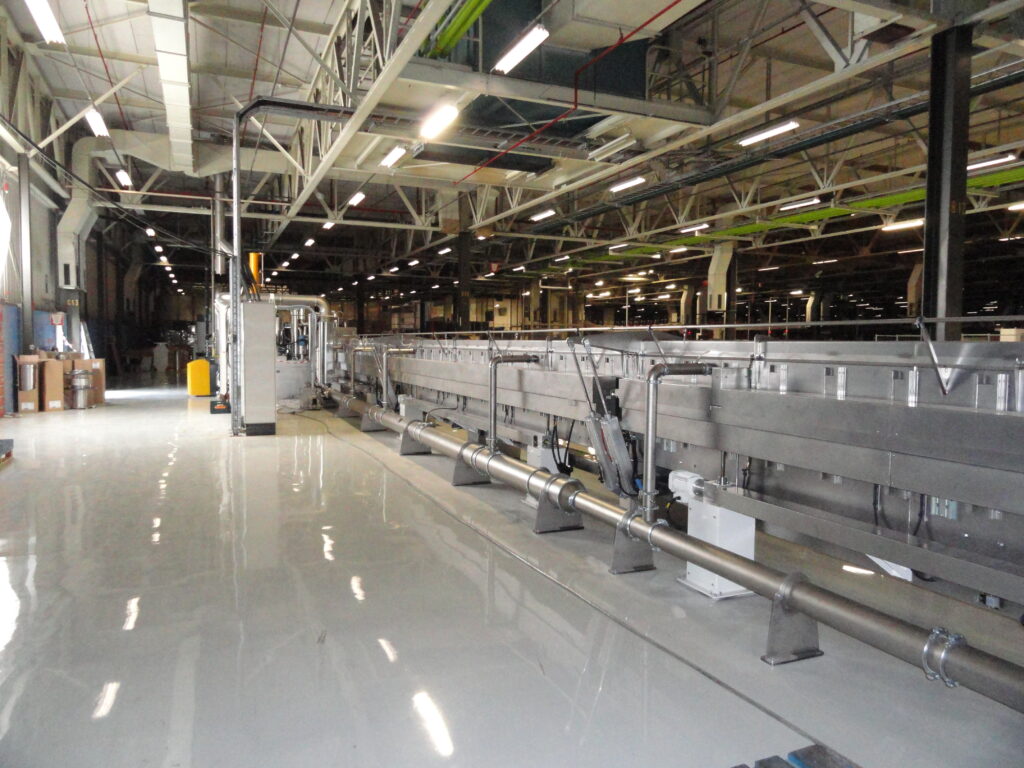
Worldwide references
With over a hundred installations in more than 85 countries for more than 20 years, including almost 32 lines applying the VulcanoClean® process and 18 VulcanoClean® adaptations to existing lines since 1995, MDC Engineering in cooperation with Durferrit®, is the leading high-tech LCM technology for the continuous extrusion and vulcanization of polymer extruded profiles, offering a safe, productive, economical system in harmony with the environment.
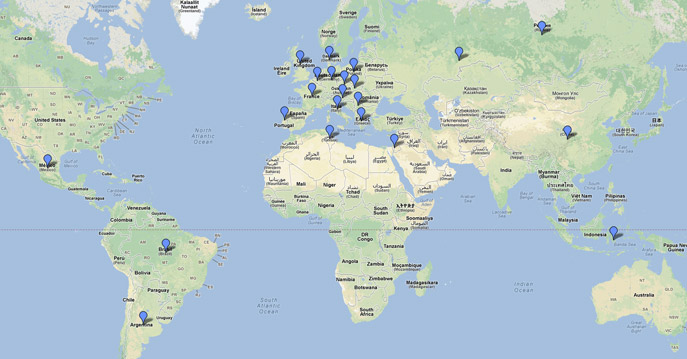